2024年7月10日(水)
1.2 炭素材料の性質を支配する構造因子
1.2.1 炭素原子の結合様式
図1.6をみて頂きたい。炭素原子はsp,sp2,sp3の3つの結合様式を有する。今更言うまでもないが,sp3炭素原子からはダイヤモンド,sp2原子から黒鉛(グラファイト)がつくられる。sp炭素原子は鎖状物質のカルビンを与える。カルビンは隕石中で発見されているが,物性測定が可能なサイズの試料は見つかっていないし,不安定なために合成されてもいない。このため性質はほとんど分かっていない。
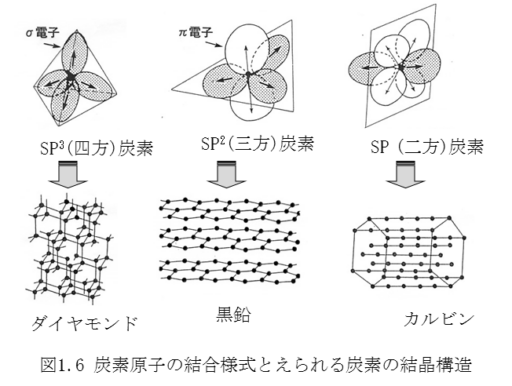
ダイヤモンドは全物質の中でもっとも硬く,絶縁体である。黒鉛はまったく逆で,柔らかくて電気の良伝導体である。この両者が共に高い熱伝導性を示すのは,一見不思議に思われるかもしれない。両者の熱伝導のメカニズムが異なるためである。黒鉛の熱伝導が層間のπ電子の移動に基づくのに対し,ダイヤモンドのそれは格子振動に起因する。ダイヤモンドの結晶構造が剛直なためである。図1.7をみて頂きたい。sp2とsp3炭素原子のいろいろな割合で構造される炭素材料が示されている。sp2とsp3炭素原子の割合を変えることで多様な構造の炭素材料を調製でき,多様な性質や機能を生み出すことに繋がる。右の図は,左図で示した種々の炭素材料の硬度と電気比抵抗を示している。
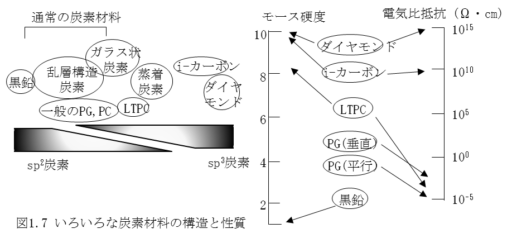
図中のi-カーボンやダイヤモンドライクカーボン(DLC)はsp3炭素原子の割合が多い炭素材料である。ただし,ダイヤモンドと違って黒色で非晶質である。性質はダイヤモンドに近く,高硬度で低い電気伝導性を示す。DLCはダイヤモンドと異なって,化学気相成長法(CVD法)で比較的容易に調製できるので,耐磨耗皮膜,潤滑皮膜や表面保護膜などとして実用に供され,このところDLKの用途は急速に拡大している。図1.7で黒鉛の隣にある乱層構造炭素の構造を図1.8に示した。図のように,黒鉛構造は層の積み重なり方に規則性があるのに対し,乱層構造は積層構造ではあるが層の積み重なり方に規則性がない。現実の炭素材料の多くは乱層構造炭素でできている。多くの性質は黒鉛に近いが,導電性や潤滑性は黒鉛ほど高くない。
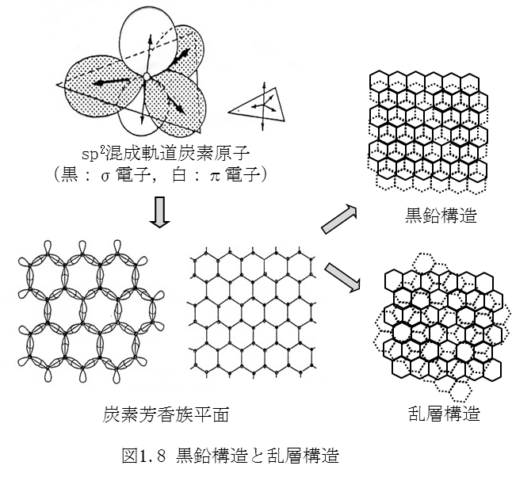
1.2.2 炭素積層面の広がりと積層の厚さ
炭素材料の構造は,原料(前駆体)とその処理条件で決まる。人間に擬えて“生まれ”と“育ち”で決まると比喩される。最初に処理温度と炭素の構造との関係,すなわち“育ち”をみてみよう。図1.9に処理温度の上昇に伴う炭素の構造変化を模式的に示した。処理温度が上昇するにつれて,炭素芳香族は平面性を向上させつつ拡大し,乱層構造を経由して3000℃近くの高温処理で黒鉛構造に到達する。
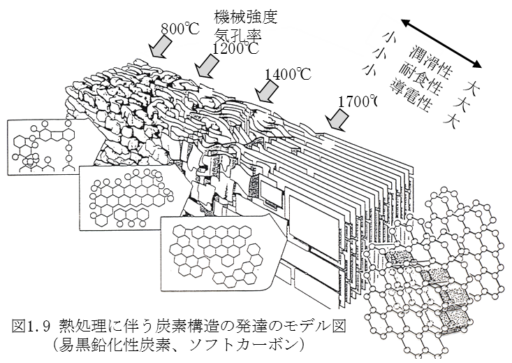
原料,すなわち“生まれ“の影響はどうだろう。図1.10に処理温度と積層構造の厚さ(Lc)および層間隔(d002)の関係を示した。実線の炭素は点線のものに比べて,温度上昇に伴うd002の低下およびLcの増大が著しい。ここには層面の広がり(La)が示されていないが,通常の炭素では,Lcの増大につれてLaも大きくなる。Laが増すと,層間を引き付けるファン・デル・ワールス(van der Waals)力が大きくなるためd002値は小さくなる。

実線のような挙動を示す炭素は易黒鉛化性炭素と呼ばれ,熱可塑性ポリマーやピッチなどのように溶融状態を経て炭になる,いわゆる液相炭素化を経由して得られる。逆に木材や熱硬化性樹脂のように固相状態のままで炭素化する原料からは,点線のような挙動を示
す炭素が生成する。難黒鉛化性炭素である。図1.11のTEM写真をみれば,両者の構造の差異
は一目瞭然である。説明が遅れたが,図1.9は易黒鉛化性炭素の構造モデルである。
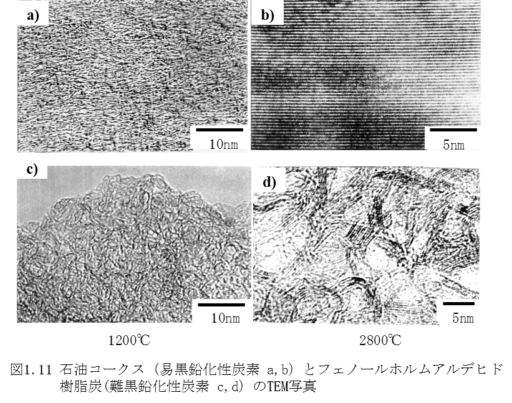
炭素の構造が図1.9のように変化すれば,当然のことながらそれに伴って性質も変化する。導電性,耐食性,潤滑性などは層構造の発達につれて向上するが,機械的強度は層間が滑りやすくなるために逆に低下する。1000℃前後で処理した炭素材料の強度がもっとも高い。また気孔率が大きくなるのも,この近辺の温度である。このように,原料の選択や処理条件により炭素芳香族平面の広がりや積層の厚さを変えることで,炭素材料の性質の制御が可能になる。
1.2.3 炭素材料中での炭素結晶子の配向
炭素材料の基本構成単位は炭素芳香族平面の積層体である。これからは“炭素結晶子”と呼ぶことにしよう。層構造に平行な方向と垂直の方向とで性質の異なることは容易に想像できる。表1.2に,異方性の異なる4つの炭素の値を示した。もっとも顕著な異方性を示すのは黒鉛単結晶で,電気比抵抗は,平行方向が0.4×104Ωcmなのに対して垂直方向は10000×104Ωcmで,実に25000倍もの差がある。加熱すると,層に垂直方向は伸びるが平行方向は逆に収縮する。これとは逆にガラス状炭素の性質は等方的である。炭素材料中での炭素結晶子の配向状態が性質を支配する重要な因子となる。その典型例が炭素繊維(CF)である。
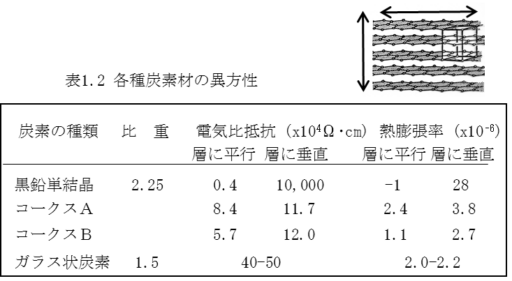
図1.12は,少々単純化し過ぎたきらいもあるが,各炭素繊維の構造モデルで,線が炭素結晶子を表わしている。CFの機械的性質は繊維の両端を固定し,切断するまで引っ張って測定される。切断時の力で引っ張り強度を,この間の伸びとから弾性率を算出する。結晶子が大きくなると,結晶子間の欠陥も大きくなるため引っ張り強度は低下する。逆に炭素結晶子の層面に平行方向は伸びにくい。このため結晶子が成長するにつれて弾性率は向上する。大きな結晶子が繊維軸に沿って配向した構造の炭素繊維が高弾性炭素繊維(HMCF)である。一方,高強度炭素繊維(HTCF)をつくるには,結晶子の配向は不可欠であるが,上述したように過度に結晶子を成長させないことが肝要であ る。通常千数百℃で処理しているのはこのためである。無配向構造の炭素繊維は,結晶成長のいかんに余り関係せずに強度,弾性率ともに小さい。低弾性炭素繊維あるいは汎用炭素繊維(GPCF))と呼ばれる。機械的特性の低いGPCFには,それなりの用途がある。
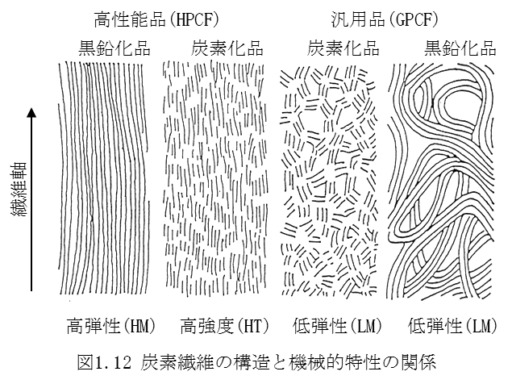
現在の CF原料の大部分はポリアクリロニトリル(PAN)で,この他にピッチがある。PAN系炭素繊維の製造過程を図1.13に示す。最初の工程は不融化(安定化とも言う)処理である。PAN繊維をそのまま不活性雰囲気中で加熱すると半融状態を示すので,空気中200~300℃前後で軽く酸化して溶融しないようにする。ついで千数百℃程度で炭素化する。しかし,特別な処理を施さなければ,炭素繊維中の結晶子は繊維軸に沿って配向しない。不融化,炭素化時に収縮するPAN繊維を収縮しないような状態下で処理する。緊張下処理と呼ばれる。実際には繊維を引っ張るのと同じ現象が生じて,平たい炭素結晶子は繊維軸に沿って平行に配向するようになる。その様子を図1.14の右上に示した。結晶子の大きさは処理温度で制御する。
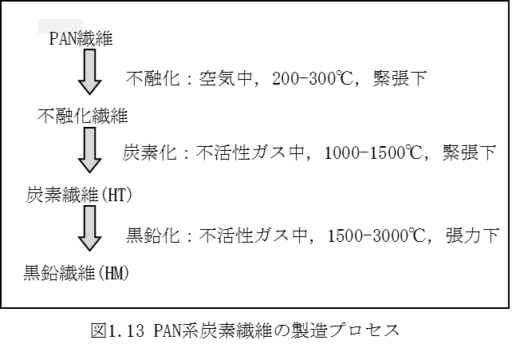
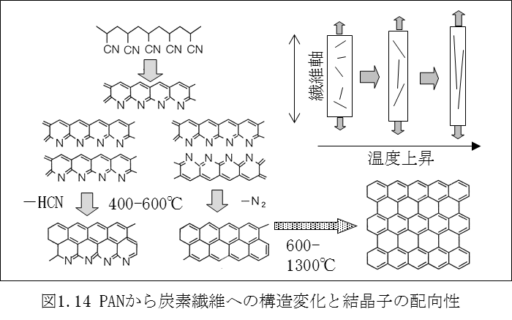
一方,細いノズル孔から溶融紡糸してつくるピッチ繊維は脆いために緊張下処理や延伸処理に供すると簡単に切断してしまう。長い間,HTCFやHMCFの高性能品はPAN系,汎用品(GPCF)はピッチ系と言われてきた。ところがピッチ系で巧みな製法が開発された。それがメソフェーズピッチ紡糸法である。
ピッチを加熱溶融すると,芳香族平面が並んだメソフェーズピッチと呼ばれる一種の液晶状ピッチが生成する。その構造を図1.15に模式的に示した。多環芳香族分子の積層体である。加熱溶融させたメソフェーズピッチを細いノズル孔から引き出す(溶融紡糸)と,右図のように剪断力によって芳香族平面が繊維軸に沿って配向する。このピッチ繊維を不融化,炭素化すれば,延伸処理を施すことなく炭素結晶子の配向したCFを調製できる。ピッチ繊維中の炭素結晶子は,PAN系のものよりも高温処理によって成長しやすいので,この方法はHMCFの製造に適している。現在は,HTCFはPAN系,HMCFはピッチ系とすみ分けされている。GPCFは等方性ピッチを用いてつくられる。HMCFやHTCFが主として補強用として使われるのに対してGPCFの主要用途は成型断熱材あるいは活性炭素繊維用など,強度をあまり必要としない分野である
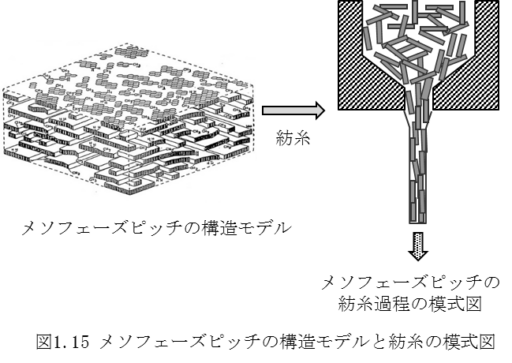
黒鉛層間に酸などを挿入してから急熱すると,挿入物がガス化して層間が拡大し,蛇腹状の膨張黒鉛が生成する。膨張黒鉛を平板間に挟み,剪断力を加えながら加圧するとフィルムになる。製造工程を図1.16に示した。フィルム面に沿って高度に配向した炭素芳香族平面間は滑りやすく,たわむ性質(可撓性:かとうせい)が発現する。この製品はグラフォイルと呼ばれ,自動車の排ガス用マフラーのガスケット(パッキング)などに用いられる。ここではグラフォイルがもつ高い耐薬品性も利用されている。グラフォイルも炭素結晶子の配向を上手に活用した炭素材料の1つである。
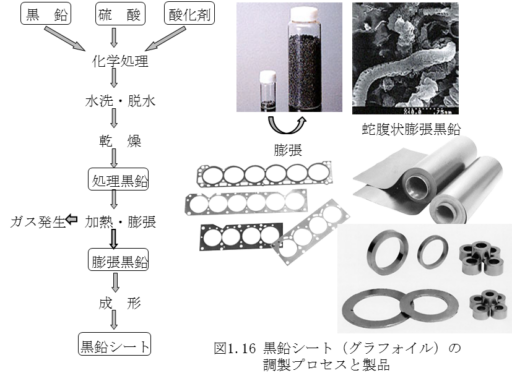
これとはまったく逆に無配向等方性の炭素材料も製造されている。高密度等方性炭素材 (HDIG)と呼ばれ,その利用分野は広く,重要な炭素材料の1つである。等方性構造が必要とされる一例を半導体製造用ヒーターでみてみよう。図1.17に示したように,切り込みを入れてつくられたヒーターに通電して発熱させる。ヒーター中を流れる電流の大きさは同じなので,炭素結晶子が電流方向に垂直に配向した高抵抗部分は,抵抗の小さな平行部分よりも高温になる。こうした温度むらをなくすには等方的な構造が望ましい。
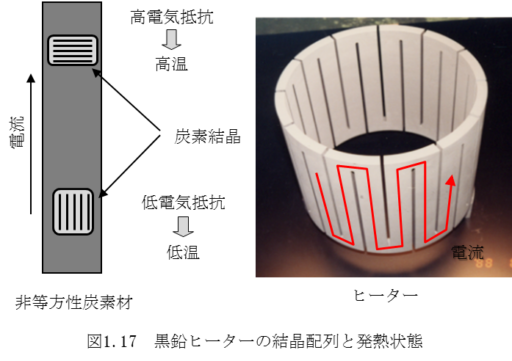
HDIGのこの他の主要用途は,放電加工用電極や冶具である。いずれの場合も,温度むらがえられる製品の欠陥の原因になる。炭素ブロックを積み重ねてつくる原子炉では,熱膨張の異方性によって炉内で応力が発生し,最悪の場合は炉の破壊につながりかねない。原子炉用黒鉛材には,高強度で膨張率に異方性のないHDIGが使用される。
HDIGは図1.18に図示した冷間静水圧法(CIP法)で製造される。原料は,通常の炭素製品と同様にコークス粒子とピッチの混練物であるが,上述した用途においては等方性構造の他に通常の炭素材料よりも均質緻密な組織も要求される。そこでHDIGの原料には,特に微細なコークス粒子が使用される。表1.2でみられるように,コークスは異方性を有する。混練物を上下から一軸加圧成型すると,コークス粒子は加圧方向に垂直に配向して異方構造が生じる。そこで混練物をゴムの袋に充填し,水中で加圧成型する。液体中なので全方向から同じ大きさの圧力がかかり,コークス粒子が配向することはない。この製法でえられる炭素材は“CIP材”とも呼ばれる。
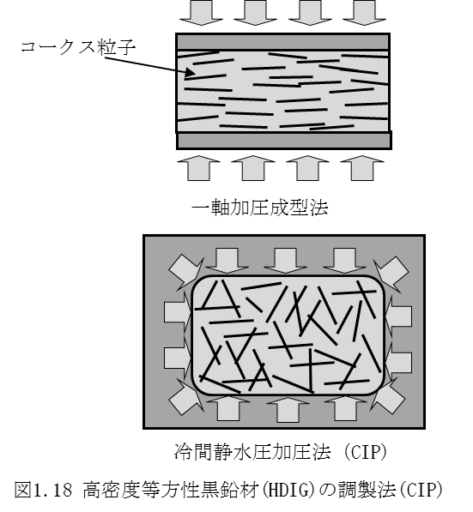
1.2.4 炭素材料の形状
製品の形状も炭素材料の性質を支配する重要な因子である。図1.19で示したように,炭素材料には0次元から3次元までの材料が存在する。0次元は点である。炭素材料で言えば,さしずめカーボンブラックということになる。小さな粒子なので大きな比表面積を有する。表面の性質を活用するには都合のよい形状である。
1次元は線。炭素繊維がこれに該当し,可撓性(たわむ性質)を示すようになる。2次元は面である。上述したグラフォイルのように,炭素繊維と同様に可撓性が現れる。3次元材料は塊。人造黒鉛電極や上述したHDIGなどがこれに該当する。剛直性を示す。
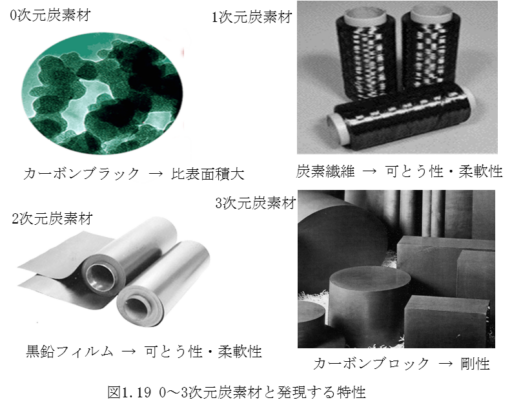
1.2.5 その他の構造因子
上述した因子以外にも,炭素材料の性質や機能を支配する因子は多い。細孔構造,表面修飾,サイズなどである。とりわけ昨今はフラーレン,カーボンナノチューブ,ナノグラフェンなどのナノサイズの炭素材料に強い関心が注がれているが,ここでは細孔構造を取り上げる。
多孔性炭素材料と言えば活性炭である。1gで1000m2もの大きな表面積を有する活性炭は,吸着剤として古くから汎用されてきた。活性炭で重要なのは,細孔径と細孔容積である。前者は被吸着分子のサイズを,後者は吸着量を支配する。
活性炭の主要原料は,椰子殻と亜炭や褐炭などの若い石炭であるが,高度利用の進展に伴い 活性炭への要求性能も厳しくなってきた。一部の要求に対しては,もはや天然原料では対応できなくなり,熱硬化性樹脂も使われるようになった。活性炭の細孔構造は,炭素材料を850℃前後で軽く酸化してつくられる。“賦活”と言い,工業的には水蒸気中で熱処理する。微細な細孔を有する特殊な活性炭の調製には,KOH,ZnCl2などの試薬が用いられる。薬剤賦活と呼ばれる。 活性炭の形状は粒状や粉状が一般的であるが,新たに開発されたのが図1.20に示した繊維形状の活性炭である。繊維状活性炭あるいは活性炭素繊維(ACF)と呼ばれ,酸化され易い難黒鉛化性の炭素繊維を賦活してつくる。椰子殻活性炭のような汎用活性炭の細孔構造は,粒子表面からのマクロ孔(>50nm),その先のメソ孔(2-50nm),さらにその先のミクロ孔(<2nm)で構成される。被吸着分子はマクロ孔,メソ孔を経てミクロ孔表面で吸着される。一方,ACFには大量のミクロ孔が繊維表面から直接に発達している。この細孔構造を反映して,ACFは吸着量が大きく,かつ吸脱着速度も大きい。こうした性質を用いて溶剤回収装置やマスクなどに利用されている。
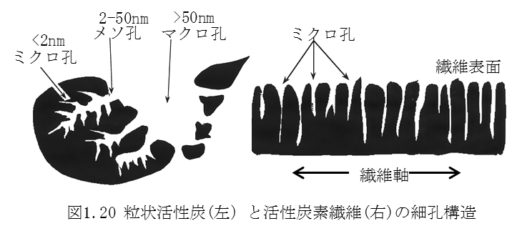
昨今,関心を集めているのが電気二重層キャパシタ(EDLC)である。図1.21に図示したように,充放電は大きな活性炭表面上へのイオンの吸脱着で行われる。この変化は,二次電池と異なり化学反応を伴わない物理変化のためにEDLCは耐久性に優れ,かつ高速充放電が可能である。こうした特性を利用してフォークリフトやクレーンなどのように,短時間に高出力を必要とする機械などで実用化されている。最近自動車の補助電源として搭載された。EDLCの最大の問題は充電容量の小さいことである。この問題を解決するためにリチウムイオン二次電池とキャパシタを組み合わせた“ハイブリッドキャパシタ”が開発され,既に上市されている。
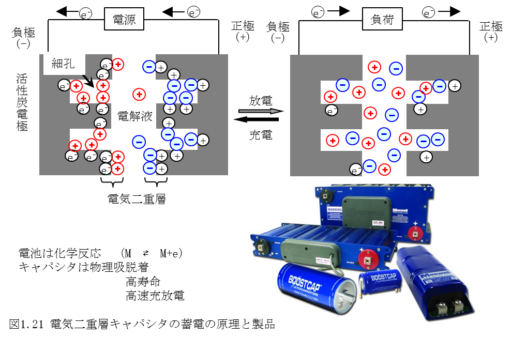
活性炭とは逆に,無気孔の炭素材料も開発されている。ガラス状炭素と呼ばれ,酸化物ガラスと通常の人造黒鉛材の中間的な性質を示す。具体的には緻密な非晶質構造や高い気体不透過性などである。3者の比較を表1.3に示した。ガラス状炭素は熱硬化性樹脂を硬化,炭素化して製造される。製造工程を図1.22に示す。ところが,熱硬化性樹脂は硬化や初期炭素化の段階で大量の水が発生し,また大きく収縮するため内部応力が発生して割れやすい。割れを回避する ために,非常に長時間をかけてゆっくりと熱処理する。それでも数cmの厚さの製品をつくるのは至難である。逆に薄手の製品ならば,大面積であってもそう問題にならない。
ガラス状炭素はその特異な構造や性質から,開発時にはその将来性に大きな期待が寄せられた。しかし低い生産性,それによる高価格化により利用分野は当初の期待に反して拡大していない。現在の主要用途は,燃料電池用セパレーターやプラズマエッチング用電極などである。電気化学の実験で用いる回転リングディスク電極もガラス状炭素である。
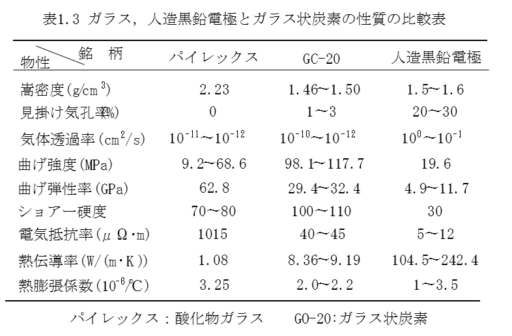
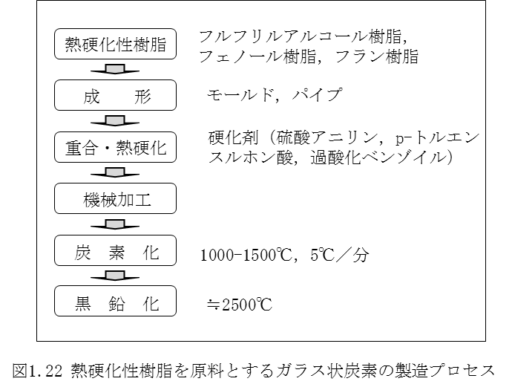
1.2.6 構造因子の具体的適応例
炭素材料の構造,そこから発現する性質や機能を支配する因子について概説した。最後に,まったく異なる性質と利用分野を有する2つの炭素繊維,高弾性率炭素繊維(HMCF)と活性炭素繊維(ACF)を例として,上述した構造因子がどのように適用されているかを表1.4にまとめた。改めて説明する必要もないかと思うが,簡単にふれておく。
まず炭素原子の結合様式である。HMCFにはsp2炭素原子が,ACFにはsp3原子が比較的多く含まれる。HMCFをつくるには,高結晶性と高配向性が必須である。sp2炭素の多い構造は,炭素結晶子の発達を意味する。弾性率を上げるのに適した構造である。しかし,成長した炭素結晶子は耐酸化性に優れるため賦活しにくい。ACFの原料としては,sp3炭素原子の割合の大きな低結晶性の構造が有利である。また炭素結晶子の基底面はエッジ面よりも耐酸化性に優れる。繊維表面に沿って基底面が配向したHMCFの構造は賦活には適さず,無配向構造の方が望ましい。両炭素繊維中の気孔の有無については説明するまでもないだろう。
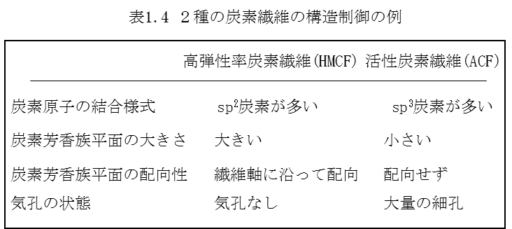
構造を支配する因子が1つ増すごとに,つくられる構造の数は倍々で増加する。ある構造因子を制御することによりAとBの相反する性質が,別の因子でCとDの性質が発現すると仮定しよう。2つの因子の組み合わせにより,AC, AD, BC, BDの4つの性質の異なる構造をつくることができる。さらにもう一つ因子が加われば,8つの構造をつくることができる。“炭素”という一種類の元素で構成される炭素材料が多様な構造,そして多様な性質や機能を示し,その上に立って多様な用途を有するのは,こうした支配因子の多いことに起因する。この点で,炭素材料は極めて稀有な材料と言うことができる。
アーカイブ
- 2025年7月
- 2025年6月
- 2024年10月
- 2024年7月
- 2024年6月
- 2024年5月
- 2024年3月
- 2024年2月
- 2024年1月
- 2023年12月
- 2023年11月
- 2023年9月
- 2023年8月
- 2023年7月
- 2023年6月
- 2023年3月
- 2023年2月
- 2022年12月
- 2022年9月
- 2022年7月
- 2022年6月
- 2022年5月
- 2022年3月
- 2022年1月
- 2021年10月
- 2021年9月
- 2021年8月
- 2021年7月
- 2021年5月
- 2020年12月
- 2020年11月
- 2020年3月
- 2020年1月
- 2019年11月
- 2019年10月
- 2019年8月
- 2019年7月
- 2019年5月
- 2019年4月
- 2019年3月
- 2019年1月
- 2018年12月
- 2018年10月
- 2018年9月
- 2018年7月
- 2018年4月
- 2018年3月
- 2018年1月
- 2017年12月
- 2017年10月
- 2017年9月
- 2017年6月
- 2017年5月
- 2017年4月
- 2017年3月
- 2017年2月
- 2017年1月
- 2016年12月
- 2016年11月
- 2016年10月
- 2016年9月
- 2016年8月
- 2016年4月
- 2015年11月
- 2015年10月
- 2015年9月